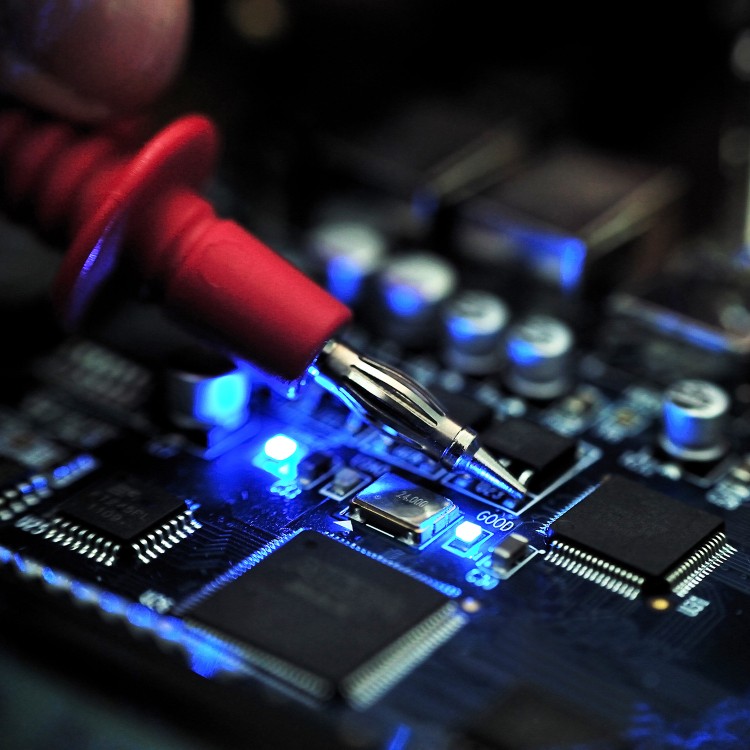
Functional Testing
Functional Testing is a crucial aspect of our comprehensive range of services at Bester. As a leading PCBA manufacturer, we understand the importance of ensuring that every electronic component and circuit board functions flawlessly. Functional Testing is a meticulous process that involves evaluating the performance and functionality of a product, verifying that it meets the required specifications and performs as intended. Our team of skilled technicians and engineers meticulously conduct a series of tests, using advanced equipment and techniques, to identify any potential defects or issues. By conducting Functional Testing, we ensure that our customers receive products of the highest quality and reliability, meeting their specific requirements and industry standards.

At Bester, we understand the importance of ensuring the functionality and reliability of your printed circuit boards (PCBs). That’s why we offer top-notch Functional Testing services to meet your specific requirements. Our experienced team of technicians and engineers utilize advanced testing equipment and methodologies to thoroughly assess the functionality of your PCBs. From performing in-circuit tests to functional tests, we meticulously evaluate each component and circuit to identify any potential faults or issues. By conducting comprehensive Functional Testing, we help you minimize the risk of defects and ensure the highest level of quality and performance for your PCBs. Trust Bester for reliable and accurate Functional Testing services that guarantee the functionality and reliability of your PCBs.
ADDITIONAL INFORMATION
How to Perform Functional Testing?
Functional testing is performed in the last step of PCB assembly manufacturing process. A functional test emulates the operational environment to ensure the PCBA’s correct functionality. The operational environment may consist of a device that communicates with the PCBA DUT. Typically, the DUT’s power supply and software test program will load the necessary parameters to make the DUT work properly.
Functional testing will verify the functionality of your PC board assembly. It will do this by applying a range of different signals and currents to stimulate the board’s behavior based on testing software developed for the board, and then measure how the PCBA reacts. It will detect both analog and digital signal problems, including distortions, incorrect currents, and signal timing issues.
The printed circuit board assembly (PCBA) may be subjected to a sequence of signals and power supply voltages. Responses are monitored at specific points to ensure correct functionality. All testing is performed according to the customer test engineer’s specifications and procedures.
PCBA Functional Testing Fixtures
Many different test fixtures have been developed for functional testing of a PCBA (PCB assembly). Electrical connections may be made with connectors present on the PCBA or by test probes that contact test points defined by the PCB designer. Connectors on a test fixture are usually modified to allow for ease of mating and de-mating of the fixture’s connectors and the connectors on the PCBA to be tested. Connectors and the connectors on the PCBA to be tested. Connectors on the test fixture are also usually made easily replaceable, since they can wear out quickly with the multiple mating and de-mating cycles of production testing.
When making direct contact to test points on a PCBA, probes under the PCBA are typically fixed and the test fixture applies hold-down force to the top of the PCBA for reliable electrical connections to the test probes. If the PCBA being tested has test points on both sides of the board, then two probe plates are required, both of which must be precision aligned to each other and to the PCBA under test. With double-sided probing, the PCBA under test is typically fixed in place and the probes move in from both top and bottom when the fixture is operated.
Why Choose Bester
Strong Assembly Capacities
With state-of-the-art facilities and a highly skilled team, we have the capacity to handle even the most complex PCB assembly projects, ensuring your products are manufactured efficiently and accurately.
Quality Assurance
Our rigorous quality control processes and extensive testing procedures guarantee that every PCB assembly we produce meets the highest industry standards for reliability and performance, giving you peace of mind and confidence in our services.
One-stop Service
From PCB fabrication and design to component sourcing and IC programming, Bester offers a comprehensive range of services under one roof, streamlining the production process and saving you time and effort.
Fast Turnaround
Our commitment to fast turnaround times means that your PCB assembly projects will be completed on schedule, allowing you to meet your production deadlines and get your products to market quickly.
Clients and Certifications
Industries We Serve
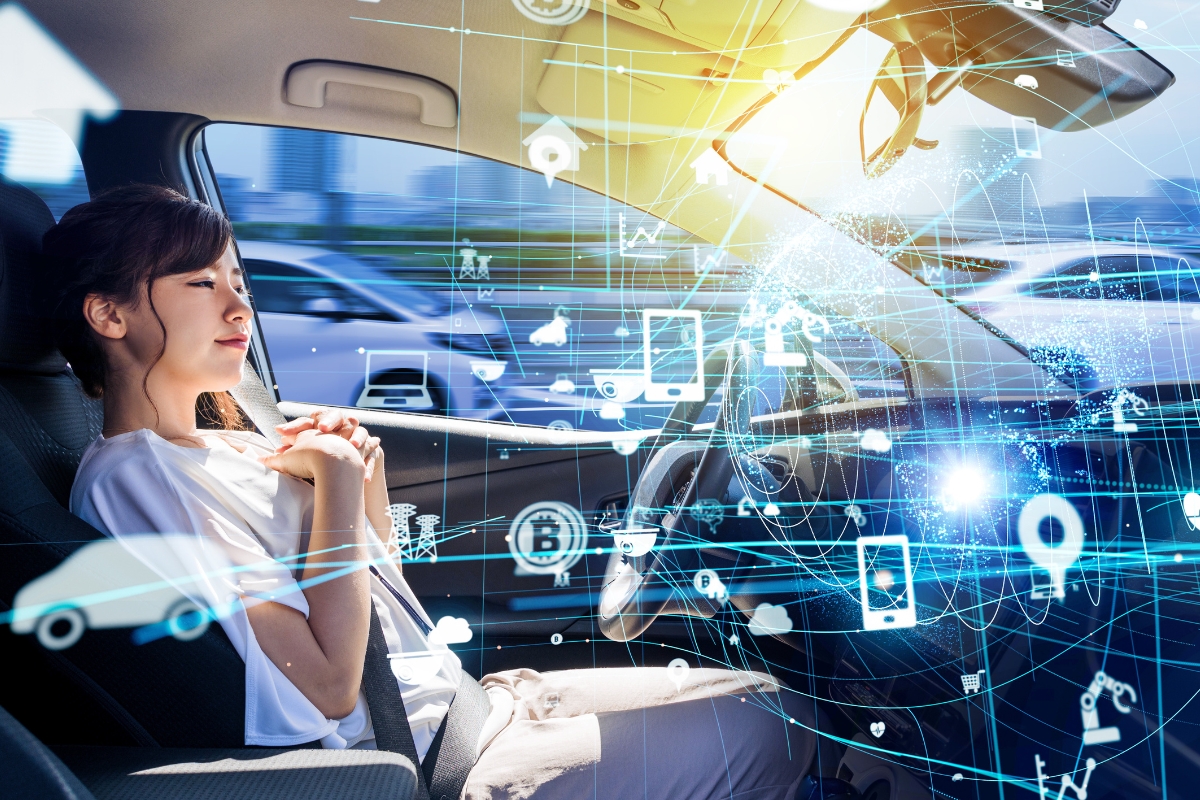
Automotive
We understand the critical role that PCBA plays in the automotive industry. With our comprehensive PCBA services, we cater to the specific needs of automotive manufacturers, helping them deliver reliable and high-performing electronic systems.
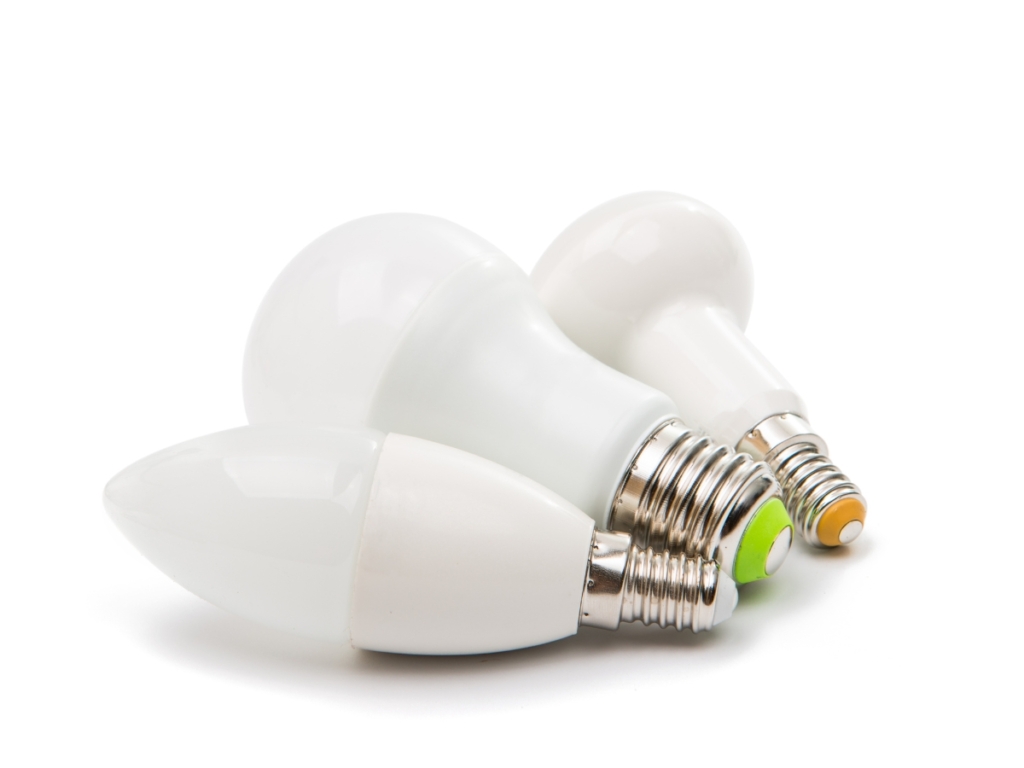
LED
In the LED market, Bester provides top-notch PCBA solutions that are essential for the production of high-quality LED lighting products. We work closely with LED manufacturers to ensure that their PCBAs meet the stringent requirements of energy efficiency, durability, and performance.
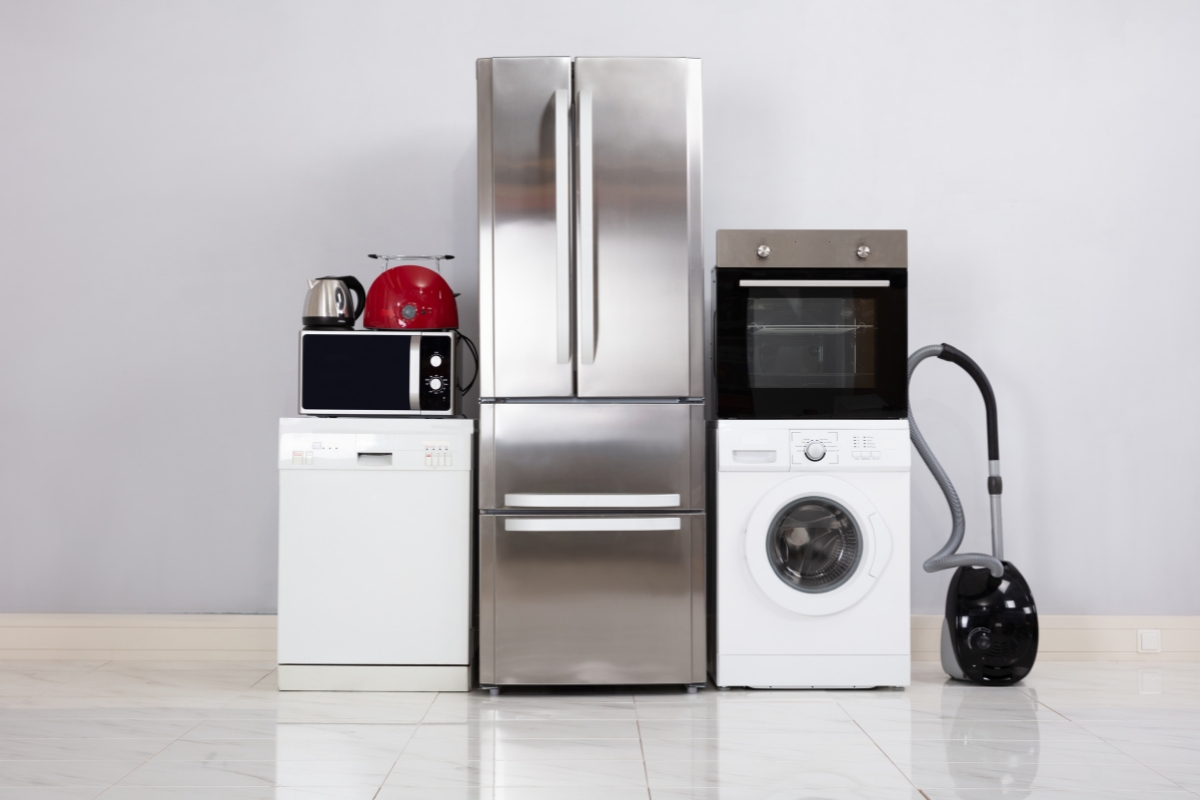
Consumer Electronics
Bester caters to the consumer electronics market by offering a wide range of PCBA services that enable the production of innovative and user-friendly electronic devices. We collaborate with consumer electronics manufacturers to ensure that their PCBAs meet the highest standards of quality and functionality.
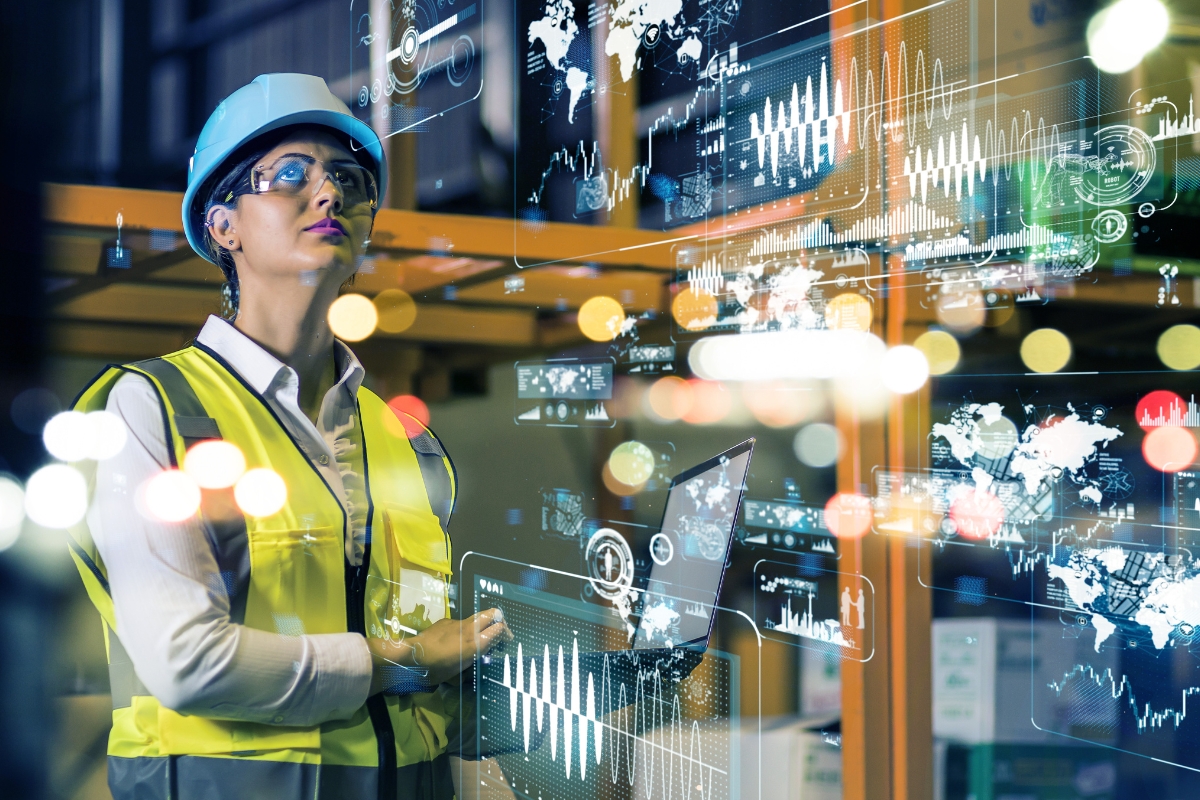
Industrial
In the industrial sector, Bester’s PCBA services play a crucial role in the development of reliable and efficient electronic systems. We work closely with industrial equipment manufacturers to meet their specific requirements, ensuring that our PCBAs can withstand harsh environmental conditions and deliver optimal performance.
PCBA APPLICATIONS
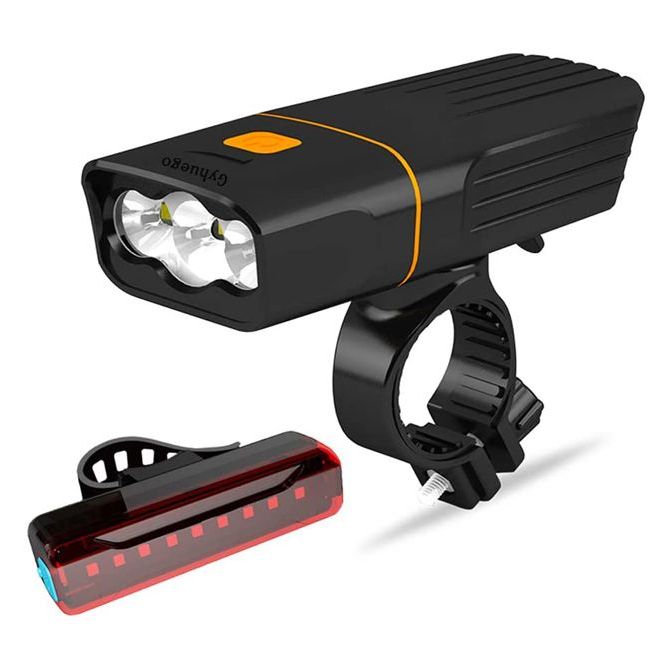
Bike Light PCBA
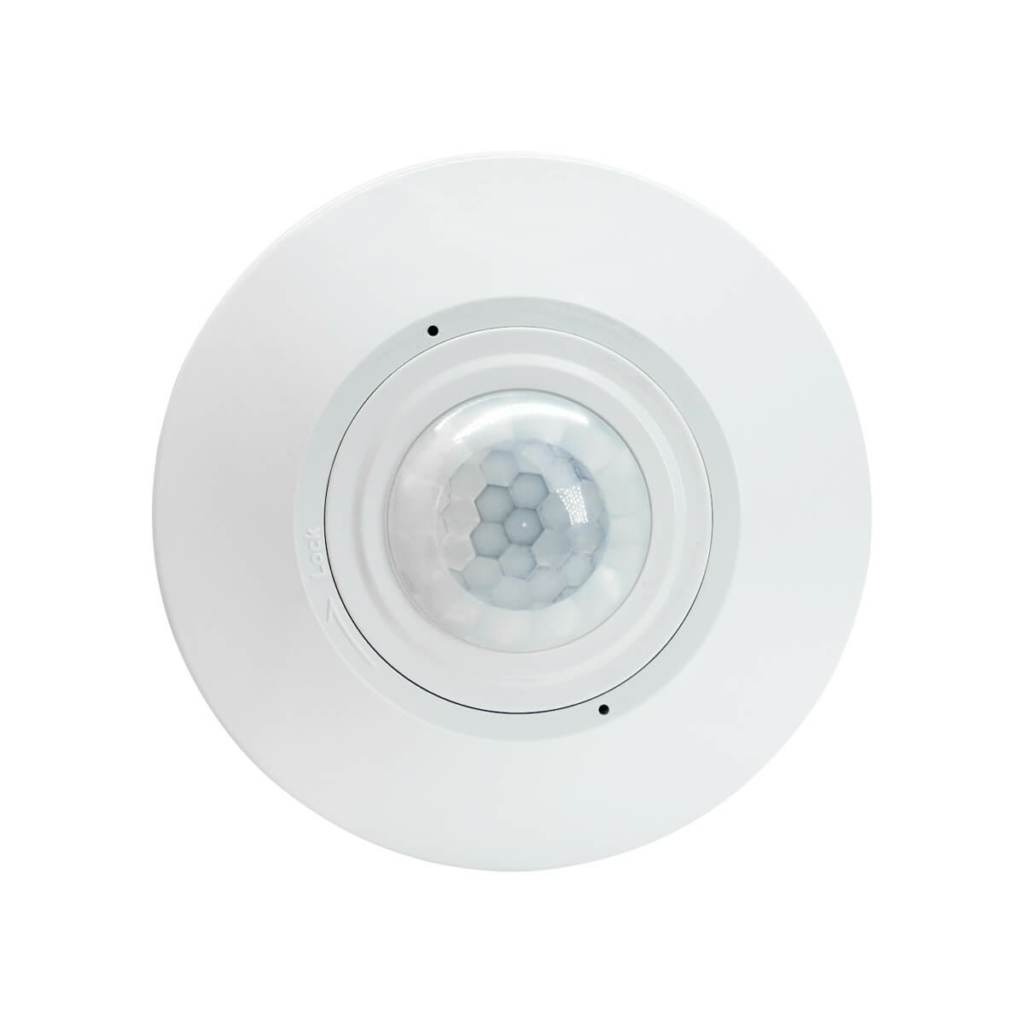
PIR Motion Sensor PCBA
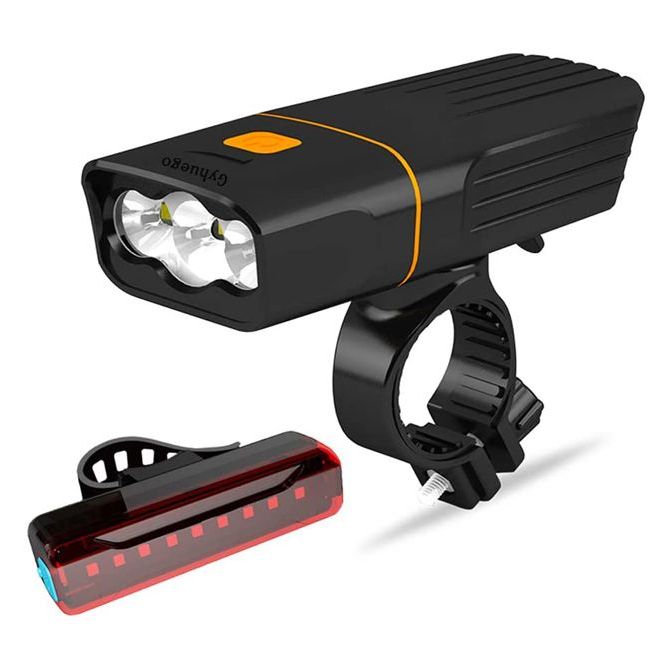
LED PCBA
PCB Assembly FAQs
Are you a certified PCB manufacturer?
Additive material process, also known as additive manufacturing, involves the123444412312312321on, such as a heated printhead or laser, to bind the layers together. Th an exact replica of the original 3D mg a fusing applicag a fusing applicaodel.
Are you a certified PCB manufacturer?
Additive material process, also known as additive manufacturing, involves the use of 3D printers to create a solid object from a 3D model. The process entails adding the material or filament layer by layer, and then using a fusing application, sug a fusing applicag a fusing applicag a fusing applicag a fusing applicag a fusing applicach as a heated printhead or laser, to bind the layers together. The end result is a 3D-printed object that is an exact replica of the original 3D model.
Are you a certified PCB manufacturer?
Additive material process, also known as additive manufacturing, involves the use of 3D printers to create a solid object from a 3D model. The process entails adding the material or filament layer by layer, and then using a fusing application, such as a heated printhead or laser, to bind the layers together. The end result is a 3D-printed object that is an exact replica of the original 3D model.
Do you offer quick turn PCBA service?
Additive material process, also known as additive manufacturing, involves the use of 3D printers to create a solid object from a 3D model. The process entails adding the material or filament layer by layer, and then using a fusing applicati
Do you accept small-batch orders?
Additive material process, also known as additive manufacturing, invg a fusing applicag a fusing applicag a fusing applicag a fusing applicag a fusing applicag a fusing applicag a fusing applicag a fusing applicaolves the use of 3D printers to create a solid object from a 3D model. The process entails adding the material or filament layer by layer, and then using a fusing application, such as a heated printhead or laser, to bind the layers together. The end result is a 3D-printed object that is an exact replica of the original 3D model.